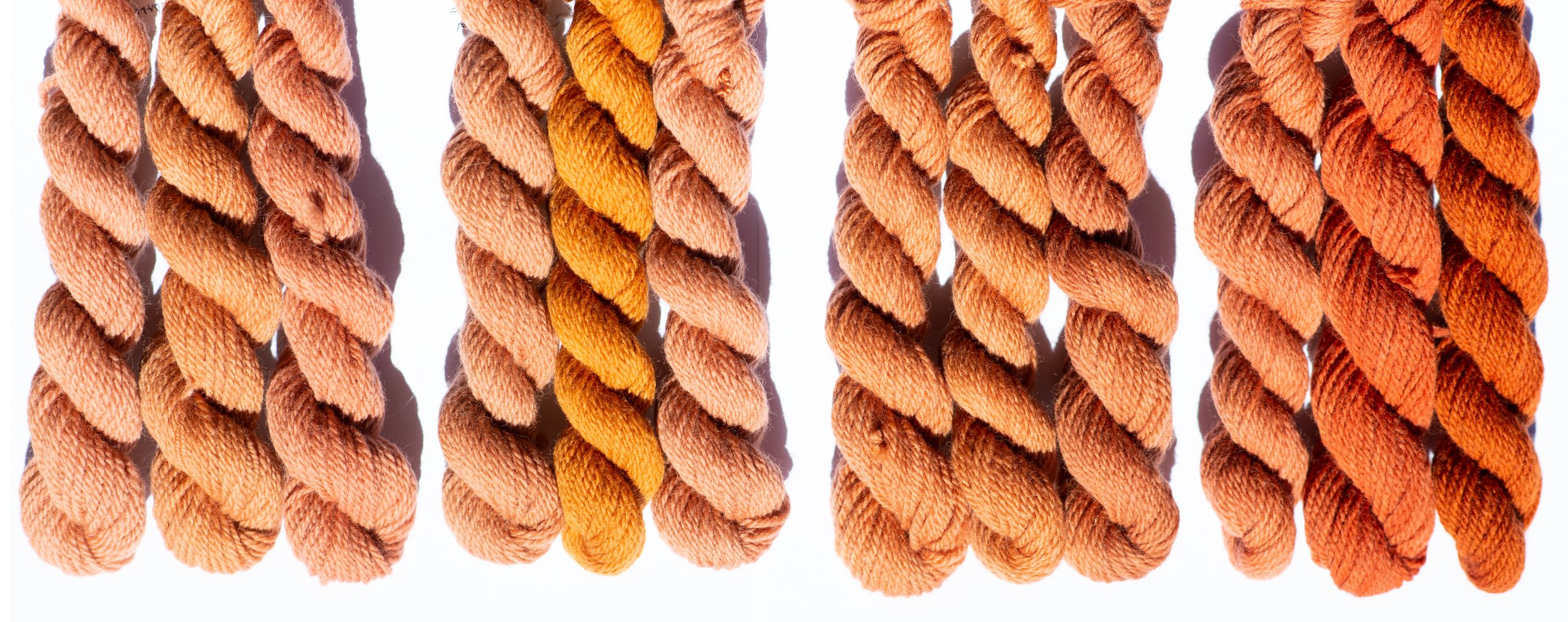
Experiments with Red Sandalwood
We spend a lot of time researching and experimenting with dyestuffs at the Shepherd Textiles studio. Our Guide to Dyeing with Red Sandalwood is the result; it shares what we think were our most successful techniques. However, there is always a lot of extra research that doesn’t make it into the published Guide, as well as many experiments that weren’t entirely successful. This page includes more detailed descriptions of our experiments and sources. We hope it will be a resource for dyers interested in digging deeper into Red Sandalwood, and perhaps improving on our methods.
Background: Research on Red Sandalwood as a Dye
One of the first things I like to do when experimenting with a new dyestuff is to Google it to see what results other natural dyers have had. However, at the time of writing there is very little published information on pterocarpus santalinus as a modern natural dye. Many of the web pages that discuss dyeing with red sandalwood actually use pterocarpus soyauxxi, a distinct species known as African Padauk or barwood. Padauk has a different chemical profile than true Red Sandalwood. Padauk heartwood contains a smaller proportion of the red santalin compounds: instead, the main pigments are santarubin A and santarubin B, a pair of related dyestuffs that are not themselves present in Red Sandalwood (Arnone et al. 1977:2116). It seemed likely that the results of dyeing with Padauk that I found on Instagram were not going to be a good indication of what to expect from dyeing with pterocarpus santalinus.
The next place I usually look for inspiration is the scientific literature. The best sources are Google Scholar (scholar.google.com), which will show all the peer-reviewed literature on a particular dyestuff; Google Books (books.google.com), which has scanned versions of a lot of 19th-century dyeing manuals; and Hathitrust (hathitrust.com), which also has a lot of old out-of-print dyeing manuals. Here, too, there was little practical information on how to use Red Sandalwood as a dye. As Pullaiah and Reddy (2019:52) note rather dryly in their recent paper on santalin, “No reliable published information is available on [the] commercial extraction process.” However, the scientific literature does contain some useful information to use as a starting point. Pullaiah and Reddy report that there are as many as five pigments in pterocarpus santalinus which give colors on textiles ranging from orange to violet to red. The most desirable is the red coloring agent, santalin, which is nearly insoluble in water but highly soluble in 90% alcohol, ether, acetic acid, alkaline solutions, and (oddly enough) lavender essential oil. However, all the papers on extracting the dye from the wood that Pullaiah and Reddy cite use either an ethanol extraction or industrial solvents like chloroform and benzene that are outside the purview of most natural dyers. After all, what’s the point of using natural dyes if they have to be extracted with something unpleasant like benzene?
Sometimes the best information on natural dyes comes from old books and journals published in the 19th century. Victorian dye manuals can be a bit disconcerting for the modern dyer, because the recipes are always for enormous quantities (“boil two hundred pounds of wool with fifty pounds of logwood, twenty pounds of copperas, and a barrel of sheep’s dung”) and because the Victorians had a real fetish for heavy metals like chromium and lead. However, they were highly experienced at getting strong colors out of natural dyestuffs. On Google Books I found a discussion of red sandalwood in an 1874 manual titled “A Practical Handbook of Dyeing and Calico-Printing” by one William Crookes. Crookes (1874:340) reports that “Santalin exhibits the following properties: — It is a beautiful red crystalline powder, almost insoluble in water, soluble in alcohol, ether, and acetic acid… alkalies dissolve santalin, yielding deep violet-red solutions, from which it is thrown down unaltered by acids. Santalin fuses at 104°.” He also reports that “Santal wood is used for some peculiar red shades upon wool and cotton after having been mordanted with alumina or oxide of tin… Santal wood dyes wool permanently, even without the aid of any mordant.” Unfortunately, Crookes’ practical handbook does not contain descriptions of the actual process for dyeing with red sandalwood, other than a suggestion that alcohol extractions were usually used. It seems that even in the 19th century, sandalwood was a relatively obscure dyestuff. However, his handbook did suggest some starting points, namely, trying an alcohol extraction, an alkaline extraction, and a tin mordant.
The next source I found useful was Arthur Perkins’ “The Natural Organic Coloring Matters” (1918), available for free on Hathitrust. Perkins (1918:612) classes Red Sandalwood among the “insoluble red woods,” and has this to say about them: “The dyestuffs of this small group, Sanderswood, Barwood, Caliaturwood, Camwood, and Narrawood, all possess very similar dyeing properties, and owing to the sparing solubility in water of the resinous colouring matters which they contain, they are called “insoluble red” woods… These dyewoods are chemically interesting in that the coloring matter present is substantive to wool, and thus, by merely boiling the material in an aqueous extract of the wood, or in a bath containing this in suspension, a brick-red shade is produced.” Perkins notes that red sandalwood gives orange-red on an aluminum mordant and red on tin (results I confirmed in my own experiments). Like Crookes, Perkins indicates that alcohol was usually used to extract the color from red sandalwood. However, he also suggests that a sort of “brute force” technique was also used, where the dyer would just boil the sandalwood in water and overcome the solubility problem by using a large quantity of sandalwood relative to wool. It was apparently effective, but wasteful: only a small fraction of the santalin in sandalwood would be applied using this method. “[A]lthough sanderswood [sandalwood] is specially rich in colouring matter, it is astonishing how little of this comes into play during the dyeing process,” he writes (1918:617). Given that Red Sandalwood is fairly expensive today, it would probably make more sense to use one of the extraction methods.
The last avenue of research I pursued was in regards to Red Sandalwood’s rarity as a dye. Why was there so little published information about a dye with such an evocative name and story? It seems that the issue is that Red Sandalwood was classified by the IUCN as “endangered” between 1994 and 2018, so it could not be legally exported as a dyestuff until just a few years ago. A report on Red Sandalwood for the Indian Council of Forestry Research (Hegde, Singh, and Krishnakumar 2012) points out that pterocarpus santalinus grows very slowly—the desirable red heartwood only begins to form when a tree is nearly 20 years old—and in their natural range the trees are highly vulnerable to forest fires, illegal logging, and depredation by cattle that graze on the leaves (2012:6-8). The heartwood is also highly desired in China for making furniture and carving trinkets, so a large black market trade exists (Arunkumar and Joshi 2014:3). As a result of all these factors, the population of Red Sandalwood trees in India was nearly decimated by the middle of the 20th century. In the late 1950s India placed export controls on pterocarpus santalinus, after which no harvesting (managed or otherwise) was permitted, and the only legal source for the wood was government sales of logs seized from poachers. In 1994, the species was designated “endangered” and in 1995 various red sandalwood products (including cut logs and furniture) were placed on CITES Appendix II, making them subject to strict international trade controls. However, the Indian government’s aggressive conservation measures appear to have been successful, and in 2018 the species was removed from the IUCN’s “endangered” list. When harvested according to government regulations the wood can now be legally sold, and it may become a more common natural dye in the future.
All this research was done in preparation for experimenting in the studio. After reading the sources I was ready to try various extractions (alcoholic and alkaline) and mordants (alum and tin) to see which yielded the best results.
Experiment 1: Just a Test
The first thing I did experimenting with Red Sandalwood was to toss a bunch into a dye pot, not paying attention to WOF, to get a sense of what I was working with. A dyeing website from India suggested using a dyebath with PH5 for both extraction and dyeing, so I acidified the bath down to PH5 with cream of tartar, let the wood powder simmer for an hour to extract some color, and then threw in a bunch of small swatches. These simmered (about 180F) for an hour, and yielded some pleasant purplish-red tones that shifted to brick red when rinsed in PH-neutral water. However, I did not filter the dyebath, which turned out to be a big mistake. With some natural dyes, you can get away with not filtering material out of the dyebath and just rinse it out of the fiber later. Red Sandalwood is not one of those dyes. Tiny, sharp bits of wood got stuck all throughout the yarn swatches, in the silk twill, and even in the fairly densely woven cotton. They would not come out, despite repeated washings. The take-away is filter all the wood out before dyeing. If the fibers were intended for actual weaving or production, I would probably have had to throw them all away.
Experiment 2: Preliminary Alcohol Extraction
The next experiment was a preliminary and fairly haphazard alcohol extraction. I did not have any grain spirits or vodka on hand, but I did have a leftover bottle of cheap tequila that had been sitting in the bar for ages—one of those tequilas so terrible it is not fit even for making margaritas. I placed 1/2 oz. of Red Sandalwood in a glass container and covered with tequila so that there was about half an inch of liquid over the wood powder. This required probably about a cup or a cup and a half of alcohol, because so much soaked right into the sawdust. I left this for about two hours, stirring occasionally. The alcohol turned a dark scarlet which was very promising. I decided to add some water into the container to dilute this extraction before adding to a dyebath, however, as soon as the water mixed with the alcohol it precipitated a thick yellow liquid that floated to the top. It almost appeared as though extraction emulsified. I later discovered that this was to be expected: in his 1874 manual on practical dyeing, Crookes (1874:341) reports that “the alcoholic tincture of santal wood exhibits the following reactions:—Addition of water causes a yellow turbidity…”. I added this now viscous-looking extraction to a dyebath and threw in some swatches (again not filtering out the wood, because I was only interested in checking the color). The results were essentially the same as Experiment 1. My hypothesis is that any clarity of color I might have got by doing an alcoholic extraction of the santalin was ruined when I added the wood to the dyebath; I should have just decanted the liquid. In both Experiment 1 and Experiment 2 the dyebaths appeared fairly murky or opaque, with what appeared to be some oiliness on the surface. My guess is that when the wood is simmered in the dyebath it extracts lots of waxes or lipids along with the various coloring compounds.
Experiment 3: Preliminary Alkaline Extraction
The last extraction method I wanted to try was using an alkali. I also wanted to figure out the best way of keeping wood out of the dyebath. I filled a dye pot with water and added enough soda ash to adjust the PH to 10. Then I put 1 oz. of Red Sandalwood powder into a large tea bag, tied it off, and tossed it into the dye bath. The results were immediately promising: a deep violet color immediately began seeping out of the wood powder, while the water remained clear rather than murky and opaque. The dyebath quickly turned a dark maroon-violet, with perhaps a strange greenish hint on the surface. I heated to 180F and maintained for two hours, then disposed of the tea bag and added some silk swatches. However, these refused to take on any color even after an hour of simmering at 160F in a deep violet dyebath. Apparently an alkaline bath keeps the santalin in solution too well. So, I adjusted the PH back down to 5 using cream of tartar. The dyebath shifted from violet to ruby red, and the silk swatches quickly took on a promising strawberry hue. However, this was late in the evening, so I turned off the heat, covered the pot, and went to bed. The next morning the swatches were a pleasant dusty pink, but they seemed to have lost some of the clear strawberry red they first took on, and they were not nearly as dark as they should have been for the amount of Red Sandalwood that was used. My take-away from this was that the tea-bag method is not effective for extracting color from Red Sandalwood powder; the sawdust needs to be simmered and stirred around to get the color out of the wood, and then filtered out of the dyebath. This experiment also made me wonder if, like madder, typical dyebath temperatures (180-190F) might be dulling the red or drawing in more of the undesirable orange and brown pigments that are also present in Red Sandalwood.
Experiment 4: Alkaline Extraction, 30% Weight-of-Fabric
With a few preliminary experiments out of the way it was now time to get serious. I filled a dyepot with warm water, adjusted the PH to 10 with soda ash, and added 1 oz. of Red Sandalwood. I simmered at 180F for one hour, then covered and let steep overnight. In the morning I filtered the dark violet liquid [Fig. 4.1] into a second dye pot and returned it to the heat. I adjusted the PH to 5 with cream of tartar, shifting the bath from violet to cherry red [Fig. 4.2]. I added 3 oz. of fabric swatches including unmordanted swatches, swatches mordanted with 12% alum, and swatches mordanted with 2% tin. Cotton swatches had been tanned with sumac before mordanting. I heated the dyebath to 185F for two hours, then allowed to cool. Swatches were lightly rinsed, dried in shade, then fully rinsed in PH-neutral detergent. This yielded pleasant terracotta colors on wool, and darker brick reds on silk. The cotton swatches appeared to have a pleasant strawberry color but dried very pale. Although the differences between mordants were not terribly pronounced at 30% WOF, tin gave a slightly darker scarlet, non-mordanted fiber a slightly lighter scarlet, and alum a noticeable orange hue. These were perfectly acceptable results, and it appeared that the acid-base extraction method was successful. However, I wanted to see if I could get the wool darker with a greater weight-of-fabric, and also if the color would stay more red and less brown if I dyed at a lower temperature.
Fig. 4.1. At PH 10, the extraction bath turns a dark violet color.
Fig. 4.2. After pouring off the liquid and filtering out the wood, adjusting to PH5 shifts the color to dark red.
Experiment 5: Alkaline Extraction, 100% Weight-of-Fabric
I repeated the experiment as above, but used 3 ounces of Red Sandalwood powder to match 3 ounces of fiber swatches. I also kept the dyebath between 140F and 150F for three hours—low and slow, like a good Texas brisket—and then allowed the fibers to cool to room temperature in the dye bath. The results were mixed. The tin mordanted and unmordanted wool swatches were no darker in color than they were in the 30% WOF bath, and their hue was not any more red. I suspect that 150F was too low of a temperature, and the dye bath for Red Sandalwood should be kept at standard temperatures of between 180F-190F to get good color application. The alum mordanted swatches, however, dyed a rich orange that was far more intense than the results from the 30% WOF bath. I suspect this was a result of the low temperature drawing in more orange pigment and less red pigment, as later dye baths I did in the 180-190F range gave more typical reddish results on alum. Both mordanted and unmordanted silk swatches gave a beautiful brick red, although in a few days this faded a bit to a red-brown. I suspected that acid-base extraction method I was using might be pulling some of the orange and brown pigments out of the sandalwood in addition to the santalin, and I hoped that with a different extraction technique it might be possible to get a clearer red from Red Sandalwood.
Fig 5.1. Results from the 30% WOF alkaline extraction on wool. From the top, mordants are wool, alum, and unmordanted. Very pleasant terracotta colors.
Fig. 5.2. Results of the dyebath at 100% WOF. I think the low temperature reduced dye uptake, except for the alum mordanted swatch, which turned a rich burnt orange.
Experiment 6: Acidic Extraction, 100% Weight-of-Fabric
I decided to attempt a more serious experiment with the PH5 extraction and dyebath, which is probably similar to the brute force method that Perkins alluded to in 1918. I filled a dye pot with warm water, acidified to PH5 with cream of tartar, added 3 ounces of Red Sandalwood, and simmered for two hours. This yielded a thick blood-red bath. When cool, I poured off and filtered the dye bath into a second pot, then returned this to the heat. I added 3 ounces of swatches including unmordanted, alum mordanted, and tin mordanted. I simmered at 180-190F for 2 hours, the let cool in the dye bath. This at first appeared to yield similar colors to the alkaline extraction. However, when the swatches dried, they were more pale and tended more toward brown than red. It was not a very gratifying outcome for using 100% weight-of-fabric, and seemed to confirm the idea that only a small amount of santalin can be extracted with water. I concluded that a simple extraction in hot water, while it does yield some nice terracotta colors, is not the best use of the dyestuff.
Experiment 7: Alcohol Extraction, 100% Weight-of-Fabric
All the old dyeing guides suggest that alcohol was usually used in the extraction of Red Sandalwood, so I tried this next. After my initial experiment with an alcohol extraction (see Experiment 2) I resolved to use a stronger source of ethanol, and to filter the wood out of the liquid before mixing with water to prevent any yellow or brown pigments from being drawn out of the wood. I put 3 ounces of Red Sandalwood in a large glass mason jar and covered with 3 cups of cheap 100-proof vodka [Fig. 7.1], the smell of which immediately reminded me of being an undergraduate. I covered the container, stirring occasionally for 2 hours, and then left to steep overnight [CAUTION: Alcohol is flammable and the vapors can cause spontaneous combustion. Keep alcohol solutions away from open flames, pilot lights, etc. Do not boil.] In the morning this yielded a dark garnet-red solution. A thin swatch of silk dipped in the solution dyed red instantly and was fast to washing—a good sign. Wool yarn and t-shirt cotton likewise dyed instantly in the tincture, and it left a coat of red stain on a steel spoon that had to be scrubbed off. Fortunately all the Red Sandalwood sawdust had settled to the bottom of the jar overnight, so I was able to carefully decant the red alcohol into a second mason jar without getting any of the wood powder mixed in. This second jar full of tincture became the base for my dye bath.
At this point I was still concerned about the “yellow turbidity” I encountered in Experiment 2 when I added water to a Red Sandalwood alcohol extraction [see Fig. 7.2]. If the turbidity was santalin precipitating on contact with water, then I might not be able to build a dyebath. If that were the case, all the coloring matter would just drop out of solution as soon as it mixed with water. However, I took a leap of faith and poured the tincture into a dyebath of lukewarm, neutral (PH 7) water. The dark garnet-red alcohol immediately turned into a cloud of milky orange. I was able to mix it into the dye bath by stirring, and the bath turned a bright, opaque orange color [Fig. 7.3]. I would later discover that the color and consistency change did not effect the dyeing properties of the extraction; swatches I dyed in this orange dyebath came out the exact same color as the swatches I had earlier dipped directly into the alcohol tincture.
None of the old dyeing manuals mention adjusting the PH when using sandalwood tincture, so I did not adjust the PH at all. However, a strip revealed that it was between PH4 and PH5, no doubt on account of all the vodka. I added 3 ounces of swatches (the usual unmordanted, alum mordanted, and tin mordanted), heated to 185F for two hours, then allowed to cool. The swatches all came out deeply saturated in rich brick-red and orange-red colors. There was really no comparison: at the same weight-of-fabric, the alcohol extraction yield vastly superior results [Fig. 7.4]. Once again, the Victorians knew what they were doing. The only curiosity was that the tin-mordanted wool came out with a slightly oranger hue, and the alum-mordanted wool with a slightly redder hue—the opposite of the expected results. However, both were richly saturated and very pleasing. I rinsed and dried inside in the shade, because I suspected that drying in afternoon light had caused some red swatches from the previous day to lose brightness and fade to brown.
The alcohol extraction was so successful that I felt no need to try other methods. I was very impressed by how powerful the raw alcoholic tincture was: it stained everything it touched a deep red, including fingers, glass, metal, and unmordanted cotton. Some day I might try making a large bucket of this tincture, say with 1kg of Red Sandalwood and a few gallons of vodka, to serve as in instant base for making red dye baths and maybe even as a cold dye bath itself.
Fig. 7.1. An alcoholic tincture of Red Sandalwood. I later transferred this to a larger jar and added a total of 3 cups of 100-proof vodka, so there would be more liquid to pour off.
Fig. 7.2. A few drops of tincture added to neutral water (PH7, left) immediately turned orange and cloudy; added to alkaline water (PH10, right) turned violet and clear.
Fig. 7.3. When the tincture was decanted in the dye bath, the bath turned orange and murky. However, fibers dyed in this bath still came out the desired brick red.
Fig. 7.4. Wool swatches from the dyebath based on an alcohol extraction at 100% WOF. These were far superior to the results from other extraction techniques.
Conclusions
After all these experiments I would make the following suggestions with regard to dyeing with Red Sandalwood:
(1) The acidic extraction is the simplest and yields usable results, but the colors tend toward pale red-brown and red-orange hues rather than saturated reds, even at 100% WOF. I would probably not use this method again, but some dyers might prefer it because it does not require a vodka soak or an acid-base reaction.
(2) The alkaline extraction is a “cleaner” extraction that gives clearer reds, especially on silk and/or with a tin mordant. It cannot match the alcohol extraction, but at 30% WOF it gives very pleasant terracotta colors that I think are good value for the money and the effort. If for some reason I did not want to do an alcohol extraction, I would certainly consider using this method again on wool—the terracotta colors would be beautiful paired with white or a light brown.
(3) The alcohol extraction gives the most saturated colors and the clearest reds. It is far superior to the other extraction methods, and the WOF can probably be varied to produce all kinds of lighter shades. I will probably keep a jar of Red Sandalwood tincture around for quick red dye baths. The only issue is that it is more expensive; it takes most of a bottle of vodka to extract 3 ounces of wood. However, a little goes a long way, and this is by far my recommended method.
Works Cited
Arnone, Camarda, Merlini, and Nasini (1977) Colouring Matters of the West African Woods Pterocarpus osun and P. soyauxi. Structures of Santarubins A and B. Journal of the Chemical Society, Perkins Transaction 1(19):2116-2118
A short and technical paper establishing the chemical structure of the santarubin compounds in Padauk wood. Probably only of interest to organic chemists, however, the introductory section explains how Padauk’s chemistry differs from Red Sandalwood (pterocarpus santalinus).
Pullaiah, T. and V. Damodara Reddy. Colouring Principle (Dye). In Red Sanders: Silviculture and Conservation (2019), eds. Pullaiah, Balasubramanya, and Anuradha, pp. 49-56.
A good overview of the state of knowledge about santalin and its extraction from red sandalwood, with a short but apparently exhaustive bibliography. One of the main take-aways, however, is that not much is really known about how to use red sandalwood for textile dyeing.
All text and images Copyright 2022 by Shepherd Textiles LLC. Do not copy or reprint without attribution and written authorization.