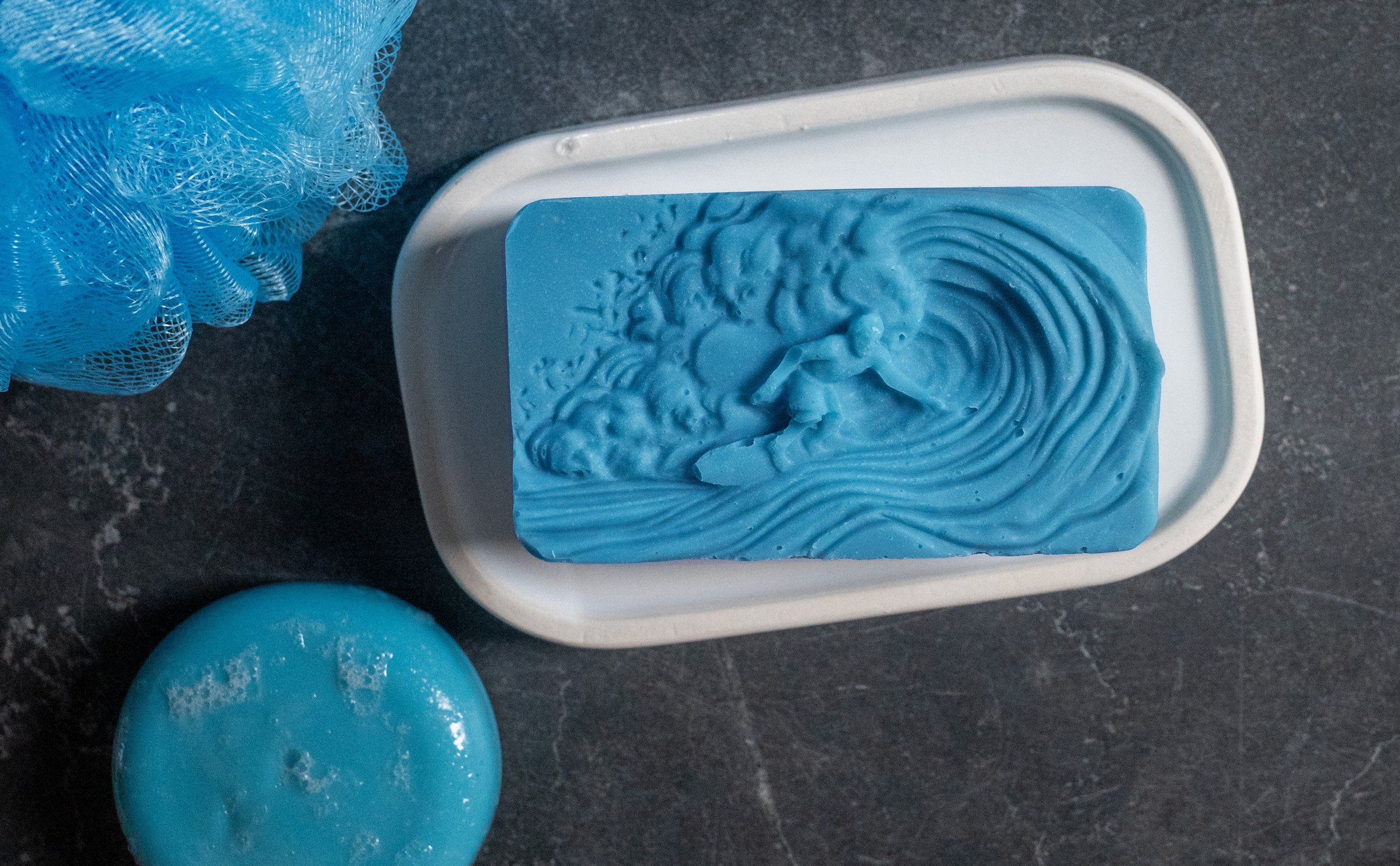
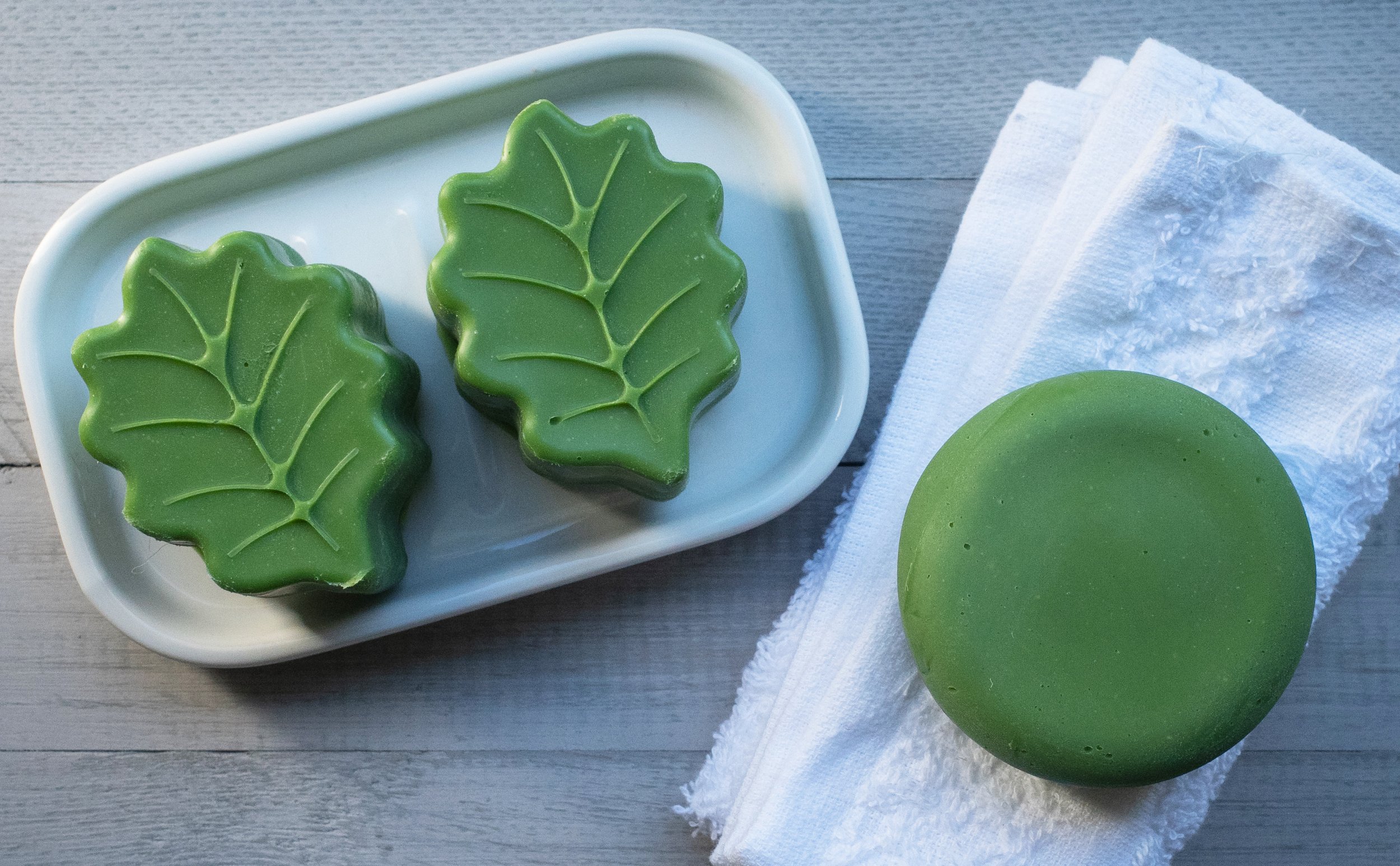
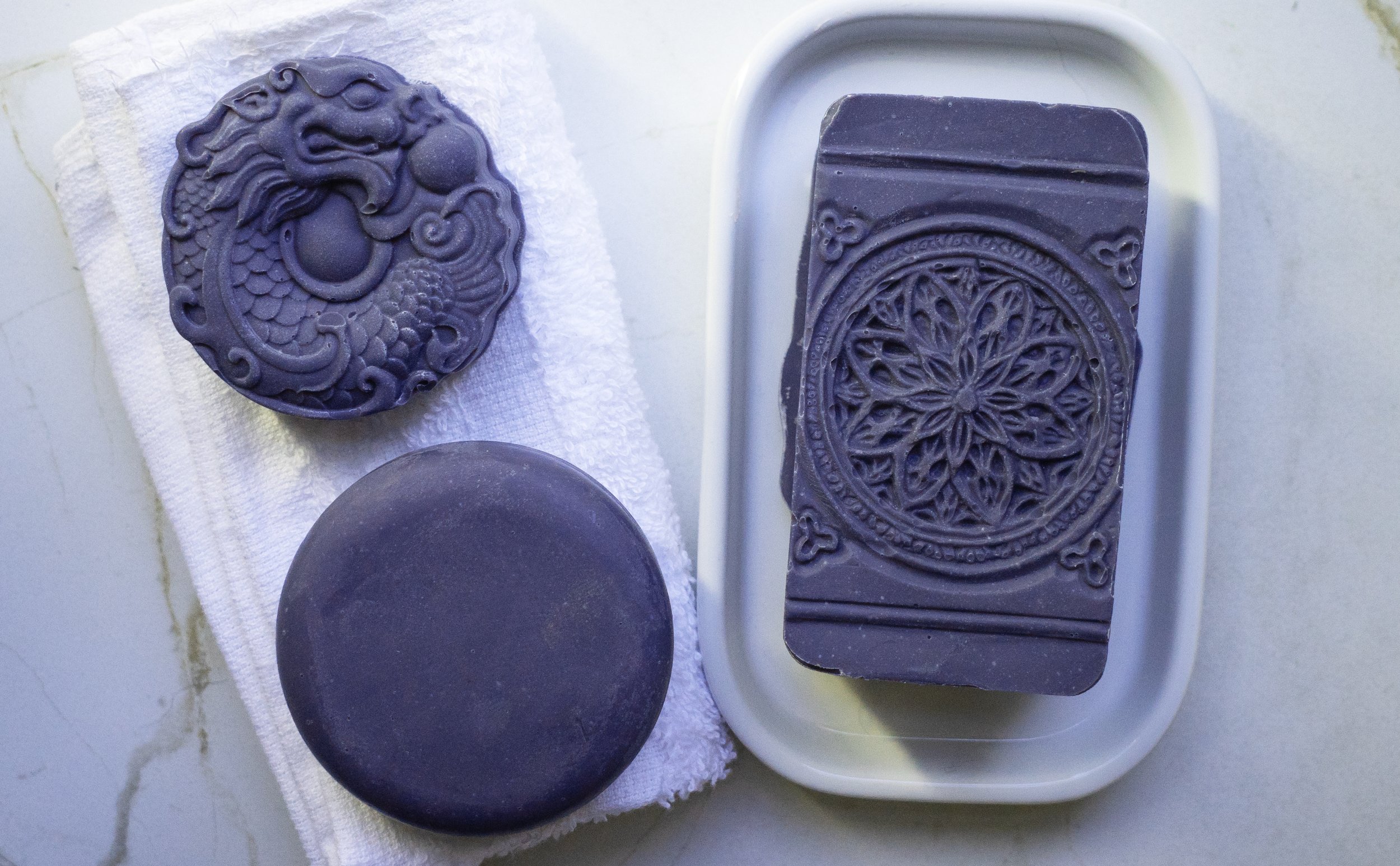
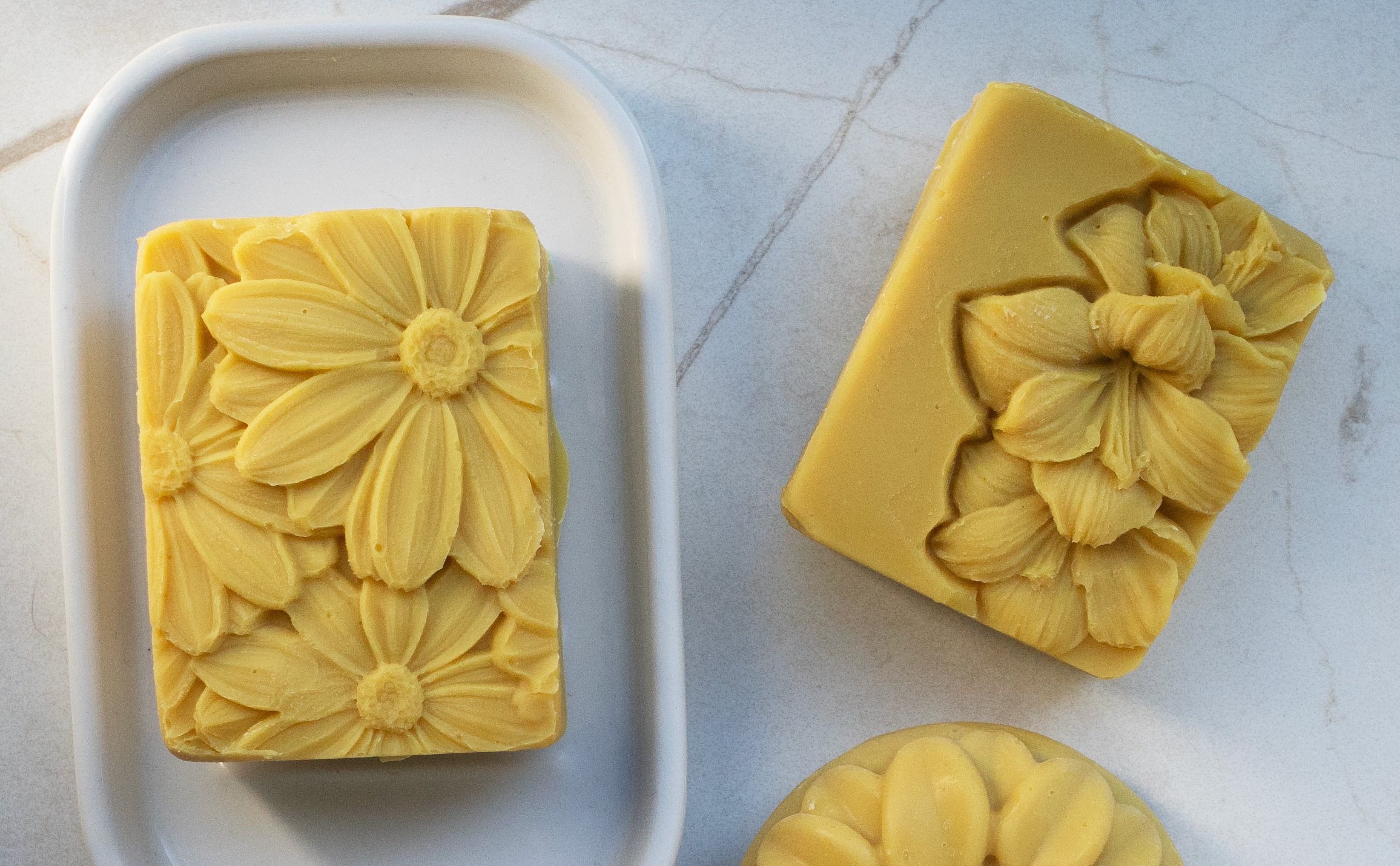
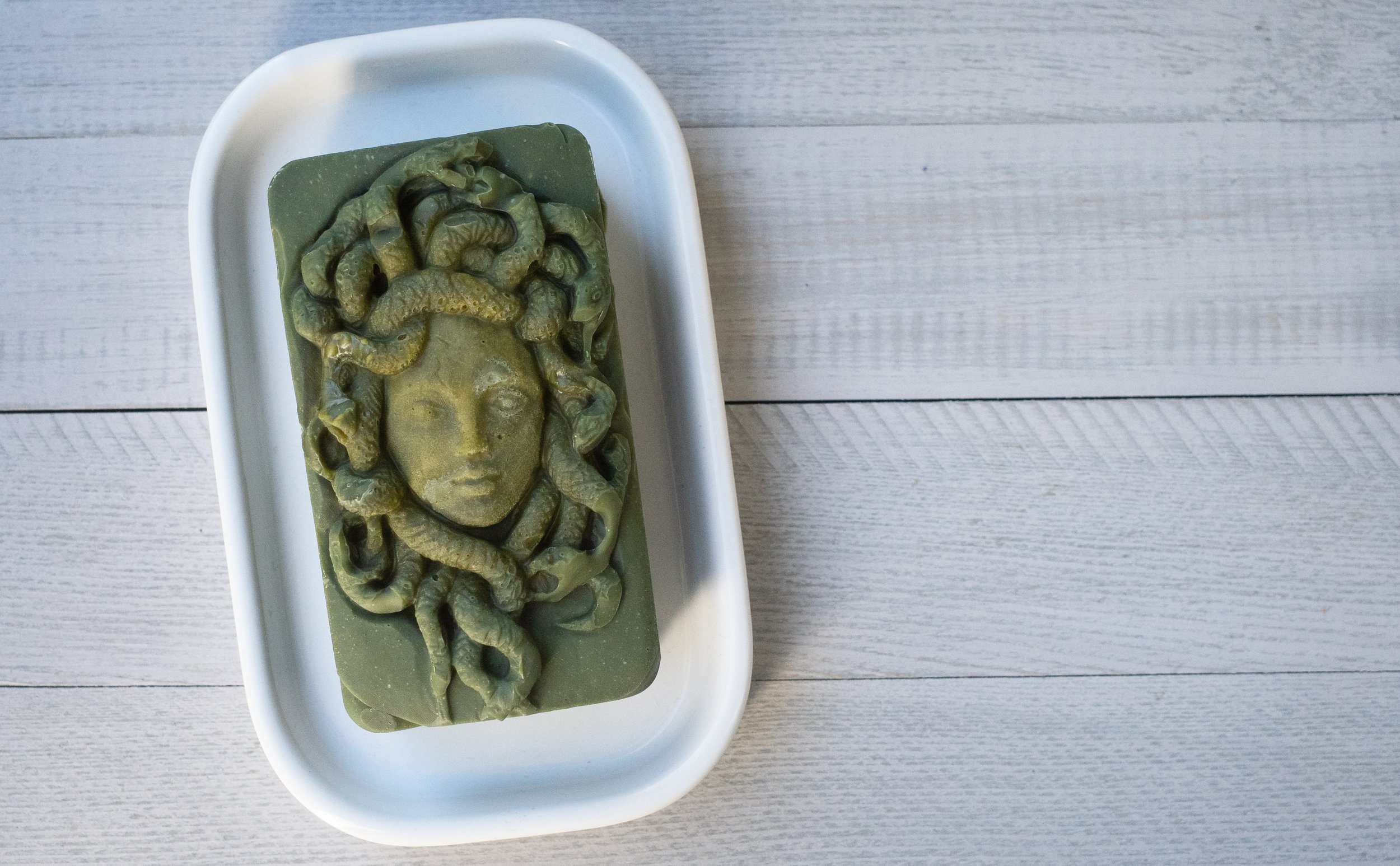
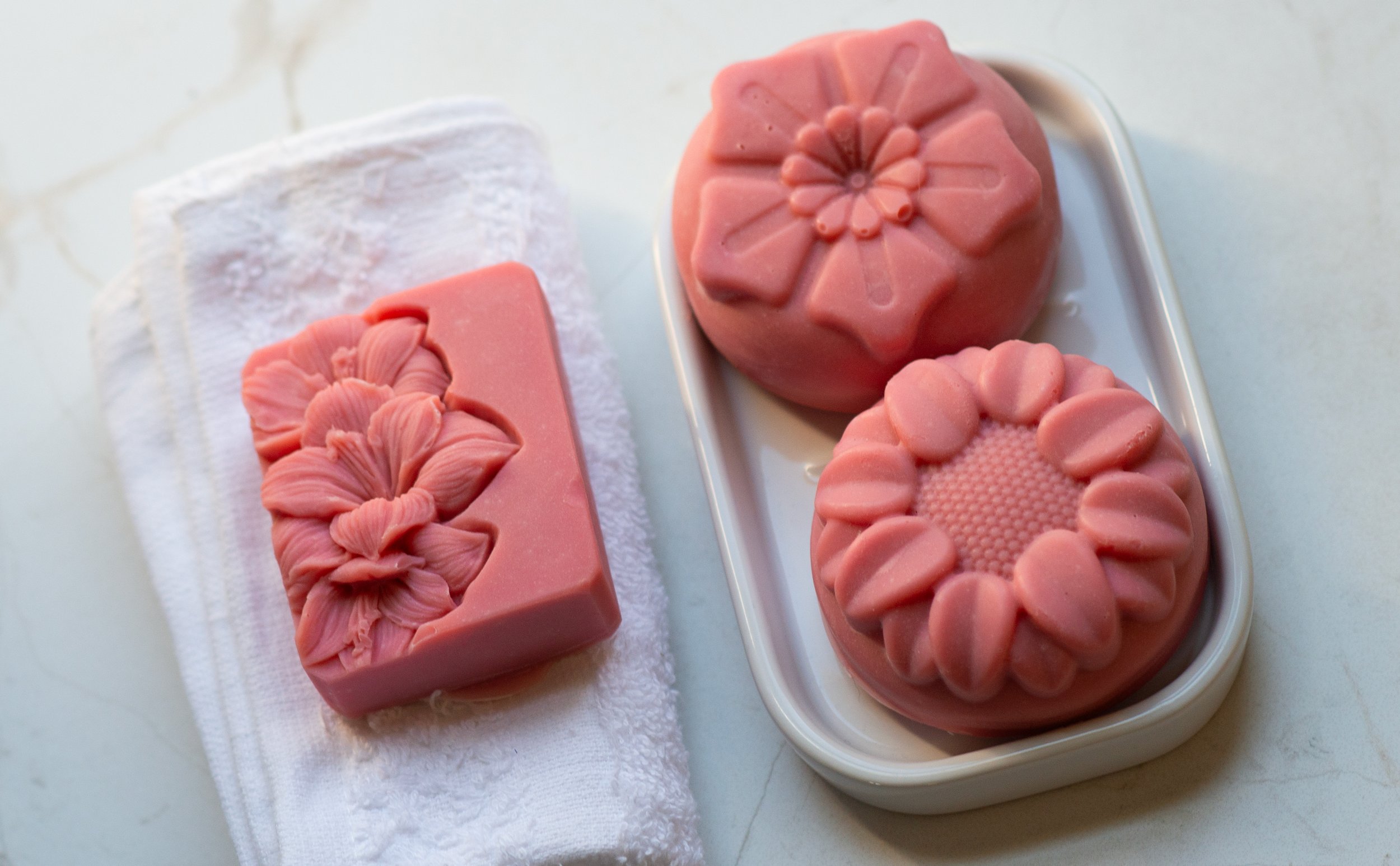
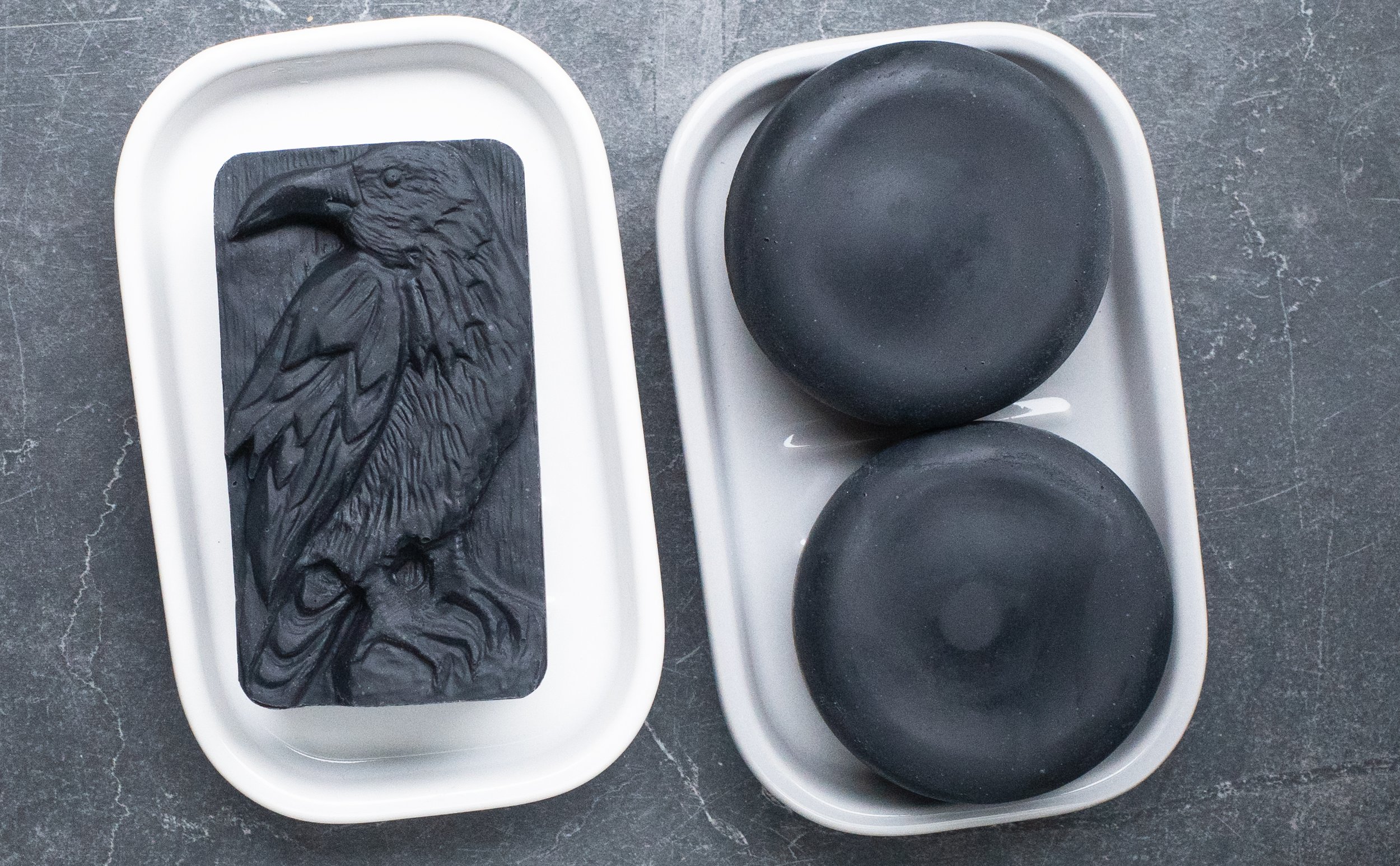
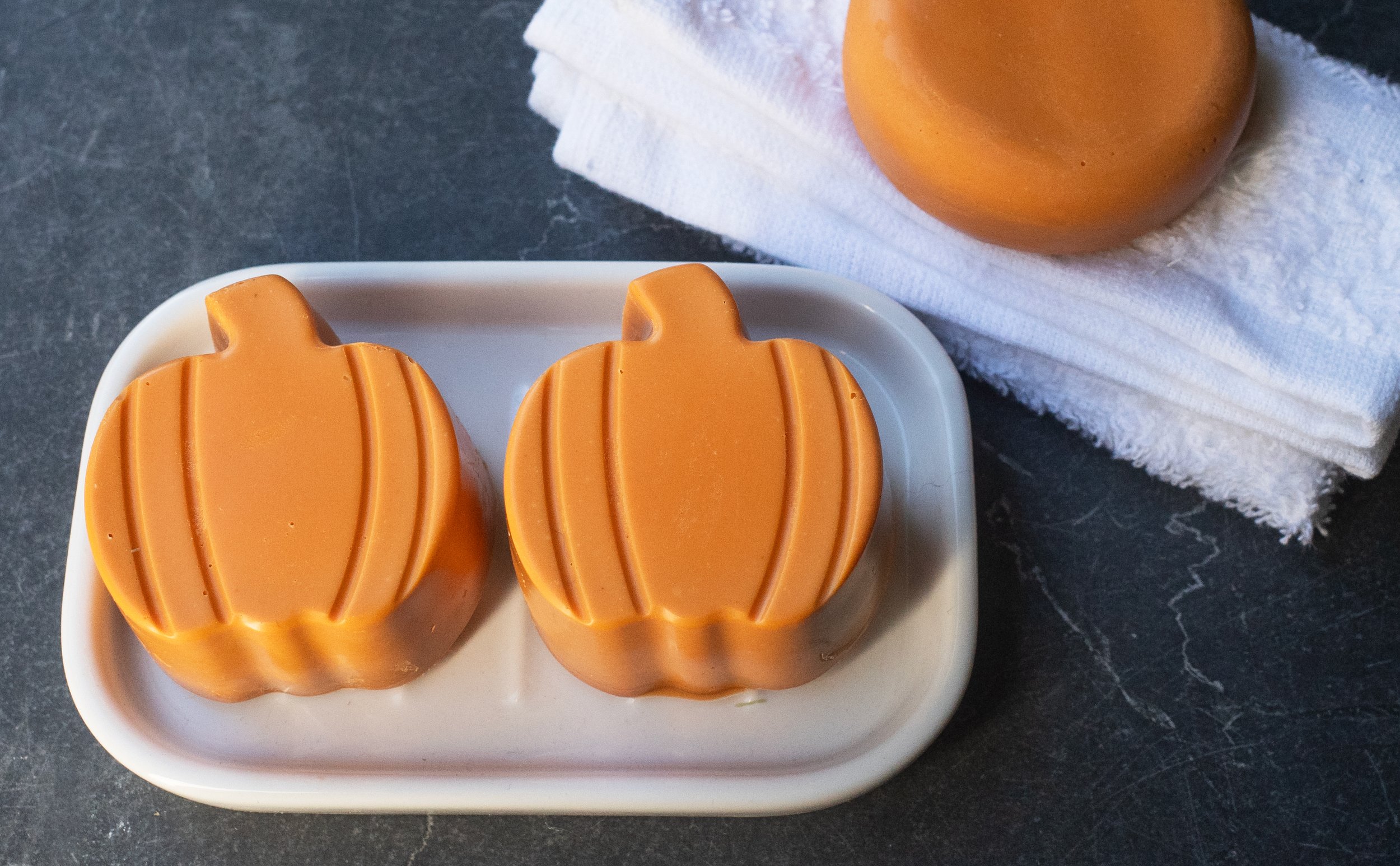
Introducing the first line of natural, plant-based pigments specifically for use in cold process soap. Made from roots, leaves, bark, and seeds, Shepherd Textiles botanical dyes will give your soap a color that’s bright, vibrant, and long-lasting. It’s time to say goodbye to synthetic chemicals on your skin.
Plant-based Natural Dyes for Cold Process Soap
Instructions:
1. Measure out 3 grams of dye powder for each pound of soap your recipe will produce (the exceptions are Ember Black and Indigo Green, which require only 1 gram per pound of soap).
2. Measure out the distilled water called for in your recipe. Add a little bit to the dye powder (about 1 teaspoon of water per gram of dye) and mix well to make a thick slurry. Be sure to break up any clumps of powder to prevent speckles later.
3. For pigment-based dyes (Madder Red, Indigo Green, etc.) mix the dissolved dye slurry back into the rest of your distilled water. Then, add the lye as usual and proceed with the recipe.
For clay-based dyes (Maya Blue and Maya Green) and for Ember Black, let the dye slurry rest and hydrate while you proceed with the recipe. Do not add it directly to the lye solution: instead, stick-blend the dye slurry into the oils right before adding the lye solution, or blend it in at trace.
4. Continue with the recipe and pour the soap as usual. To prevent fading, cure and store out of direct sunlight. Note that natural dyes are pH-sensitive and the color will change and develop as the soap cures. For example, Madder Red soap will look purple-brown when first poured, but will cure to strawberry red after a few days. Enjoy!
Safety Precautions
Our plant-based soap dyes should only be used in traditional cold process soap. They should not be used in food products, cosmetics, or soaps that are marketed with medical claims (for example, a soap that claims to cure psoriasis).
Always wear a mask when working with dry pigments. Work in a space with good ventilation, and avoid inhaling any dust.
Using more than the recommended amount of dye may result in soap that produces a dark lather that can stain light-colored towels. Shepherd Textiles is not responsible for any unintentional staining of towels or other property.
Do not ingest. Avoid direct contact with eyes; in case of eye contact, rinse well with cool water. Wash hands after use.
Plant-based dyes may cause skin irritation or allergic reactions in individuals with specific plant allergies. Always notify customers when plant dyes are used, so that they can avoid allergy triggers. If irritation occurs, discontinue use.
Keep out of reach of children.
The lye used in soap making is highly caustic. Be sure to read your vendor’s Safety Data Sheet before using lye, and observe all recommended safety precautions. Wear gloves and face protection when handling lye, lye solution, and soap batter.
Frequently Asked Questions
-
We believe in complete transparency when it comes to dyes that will come into contact with your skin. That’s why we list all of the ingredients in every dye we sell; nothing is hidden as a “trade secret.” Most of our dyes are pigments produced from just three ingredients: a plant extract, alum (potassium aluminate sulfate), and washing soda (sodium carbonate). The alum combines with the plant dye to form a lake (a particle of color) and washing soda, a weak alkali, helps it to precipitate (undissolve). Ember Black is pure cosmetic-grade softwood charcoal, while our Maya Blue and Maya Green dyes are made from indigo and natural sepiolite clay. And that’s it. Just plant extracts, alum, washing soda, and clay.
-
In the USA, all cosmetics are strictly regulated by the FDA. Only colorants that have been evaluated and approved by the FDA are allowed to be used in cosmetic products. The FDA maintains a short list of approved colorants here. Many of the approved colorants are synthetic chemicals like D&C Red #21, which developed out of research on coal-tar colors in the 1800s. The only natural colorants currently on the list for cosmetics are carmine (the alum lake of cochineal) and annatto. Since the natural colorants we use (like madder lake and weld lake) have not been evaluated or approved by the FDA, they cannot be used in any FDA-regulated products. However, traditional cold process soap is not regulated by the FDA, so our natural dyes can be used in your cold process soap so long as it is not marketed with any medical claims (at which point it would be considered a medicinal product and would fall under the FDA colorant regulations).
-
Our soap dyes are made from insoluble pigments (color lakes and clays), while our textile dyes are mostly water-soluble extracts. Pigments have several advantages as soap colorants: they produce deep colors in cold process soap and they are less likely to bleed when washed. Also, textile dyes often contain organic plant matter (like tiny bits of root or bark) that don't cause any issues in a dye bath, but can cause unsightly speckles in a bar of soap. In contrast, our soap dyes will create even colors so long as they are dispersed completely into the soap batter.
-
Plant-based natural dyes are not as lightfast as synthetic dyes, and direct exposure to sunlight will eventually cause them to fade. This is usually a result of UV rays breaking down the bonds that hold together the color particle. Most of our soap dyes can withstand about a week of direct sunlight before noticeable fading occurs. However, the color will remain bright and vibrant for up to a year or more so long as the soaps are stored in a dark place or under artificial indoor light. For that reason, we recommend curing and storing soaps colored with natural dyes out of direct sunlight (and definitely not sitting on a window sill!). However, if you need a soap that never fades we recommend Maya Blue, which in theory can survive a few centuries of sunshine without losing any color.
-
We recommend dissolving most of our dyes in the lye water solution because the heat and alkalinity will help them to dissolve more evenly (exceptions include Maya Blue and Maya Green, which are clay-based pigments). However, you can always add the dyes at trace — for example if you want to divide up the batter and make each portion a different color. The main challenge will be getting the powder to fully disperse in the oils without any big clumps, which can cause dark speckles when the soap cures. If you need to add the dyes at trace, we recommend mixing them with a small amount of distilled water to make a thick slurry (you can reserve some water from the main recipe before adding lye, if you don’t want to worry about water discounts). This will give you a chance to break up any clumps; then you can add the slurry to the soap at trace and stick-blend it in. However, note that some dyes like Quebracho Brown can accelerate trace, so you may need to blend them in pretty quickly.
-
It is not necessary to force gel phase; none of our example soap bars went through gel phase. Forcing gel phase can result in slightly deeper colors in cold process soap (and sometimes different hues) but we have not tried it with our own dyes. However, if you give it a try, we'd love to hear about it! Our only caution is that you may get unexpected results with compound colors like Indigo Green, where gel phase can affect the indigo differently than the annatto.
-
All of our example bars were made with a three-oil base consisting of vegetable shortening, coconut oil, and olive oil. This has quickly become our favorite oil base because all the oils are available at the grocery store, and it produces a bar that hardens quickly without any additives. We have had the best results combining the lye solution and oil at 110F-120F. Since we usually use detailed silicone molds we usually pour at a fairly light trace, and leave for 48-72 hours before unmolding.