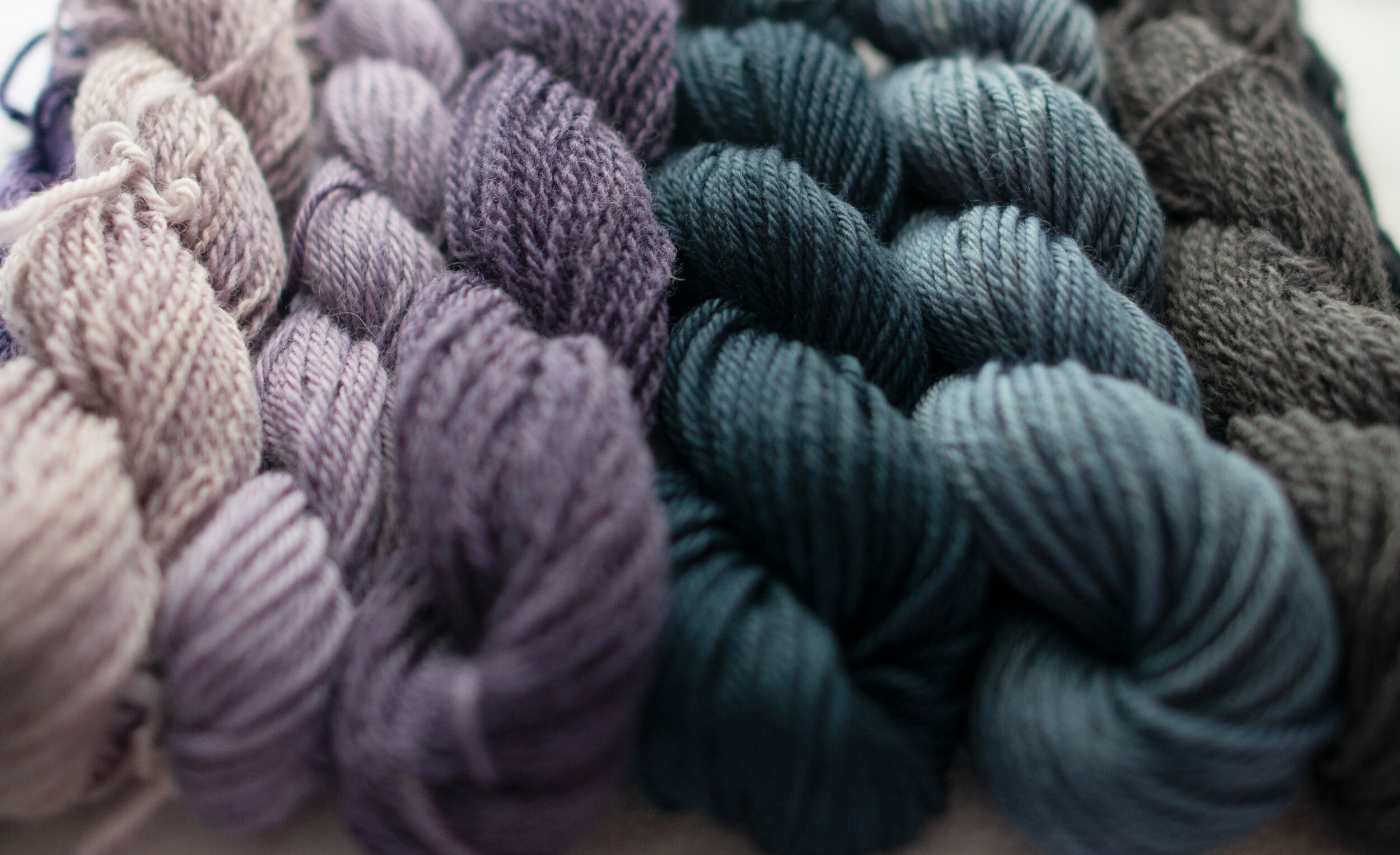
Royal Logwood Extract
A Guide to Royal Logwood Extract
Shepherd Textiles Royal Logwood Extract is made from haemotoxylin campechianum, the Campeche Logwood tree. The tree’s heartwood is rich in a potent dyestuff called hematine. Hematine has an exceptional affinity for natural fibers like wool and cotton, and it will dye well-mordanted fibers very quickly. The color can be changed by using different mordants—alum gives royal purples, copper gives somber blues, and iron yields grays and blacks. Our Royal Logwood Extract is made in the USA from sustainably harvested Mexican logwood. This grade of logwood extract is often used for dyeing medical sutures, and is very strong. Use at 2% weight-of-fabric (WOF) for rich royal purples and midnight blues.
1. Background on Logwood
The logwood tree, haemotoxylin campechianum, is native to southern Mexico and the Yucatan peninsula. Its use as a dye was well-known to the prehispanic Maya, and Spanish explorers began trading for it as early as 1502. Logwood quickly became one of the major exports of New Spain, along with silver and cochineal, because for several centuries it was the only reasonable source of purple and black dye. Contemporary sources describe Spanish galleons crossing the Atlantic with the decks piled high with logwood timber, and logwood ships were one of the major targets of English pirates along the Spanish Main (Ortiz-Hidalgo and Pina-Oviedo 2019:4). The port of Campeche on Mexico’s Gulf Coast controlled most of the logwood trade in the 17th and 18th centuries, hence why logwood is sometimes referred to as Campeachy Wood. The botanical name, haemotoxylin, is Greek for blood-tree, referring to the dark color of the heartwood after it oxidizes.
The heartwood of the logwood tree contains a potent compound called haemotoxylin. After it is extracted by boiling (or, today, by steam extraction) it is exposed to air and oxidizes into the pure dyestuff called hematine. Hematine is a powerful dye on all natural fibers, even cellulose fibers like cotton that are often resistant to natural dyes. However, it requires a mordant to bond effectively to fiber. Alum gives rich purples, although they have a reputation for fading in sunlight. Copper yields blues that Victorian dyeing houses celebrated for their strength and lightfastness. Iron gives grays and true black. Logwood was mostly abandoned after aniline black dye was invented in 1865, but it is still used today to safely dye medical sutures black so they can be seen more easily.
2. Safety Precautions
DO NOT INGEST. This extract was prepared for textile dyeing, not as an herbal supplement.
Avoid eye contact. If eye contact occurs, rinse with cool water.
Not for use as a cosmetic additive; do not apply directly to skin or hair.
Open carefully to avoid spilling or creating dust.
If a spill occurs, quickly wipe up with a paper towel or disposable rag.
Royal Logwood Extract can permanently dye clothing, countertops, rugs, utensils, or other property. Avoid contact with anything that is not meant to be dyed.
Use only dye pots and utensils dedicated to dyeing. Do not use any pots, containers, spoons, tongs, thermometers, or other utensils that will be used for food preparation.
Copper powder and iron powder are both irritants and may be harmful if ingested. Read your manufacturer’s safety data sheet (MSDS) before using copper or iron as a mordant.
Royal Logwood Extract, and all dye baths and mordant liquors made while dyeing, should be kept out of reach of children and pets. Use only with adult supervision.
Shepherd Textiles, LLC is not liable for any misuse of this product or any unintended staining of your clothing, workspace, or other property. Use only as directed.
3. Recommended Supplies
Dye pot. Use a dye pot large enough to hold all your fibers, with plenty of room for them to move around and for the liquid to circulate freely. Logwood extract may leave faint stains on metal dye pots. If so, the stain can usually be scrubbed out with a scouring pad.
Metal tongs. A pair of tongs is useful for stirring and taking fabric out. Use tongs dedicated to dyeing, and not for food preparation.
Rubber gloves. Wear rubber gloves while handling extract powder and while handling mordanted/dyed fiber before it is rinsed.
Candy thermometer. Royal Logwood will lose some of its clarity if the dye bath gets hotter than 175F. The best way to keep track of temperature is to use a cheap candy thermometer that clips to the side of the dye pot.
Scale. Use a scale to weigh out fiber, mordant, and extract powder.
Alum, copper, or iron mordant. The color produced by logwood is determined by the mordant used. For purples, use aluminum potassium sulfate, also known as potash alum. It is the same alum that you can find in a jar in the spice section at the grocery store.
PH strips. For adjusting the dye bath PH.
Disposable cup. For mixing the extract powder to a paste.
PH strips and a candy thermometer make it easier to control the dye bath.
4. Preparation: Mordanting
Logwood only bonds effectively to fibers that have been mordanted; otherwise it just produces a faint brown. Alum, copper, and iron mordants will all yield different shades. For best results, soak your fibers in water for a few hours before mordanting, so that the mordant will penetrate deeply and evenly. Make sure to weigh the fibers first, while they are still dry.
Mordant powders will dissolve quickly into hot tap water.
Heat fibers to 180F.
For protein fibers (wool, silk, alpaca): Mordant at 12% WOF with alum or 2% WOF with copper or iron.
Weigh out the fibers you plan to dye (while they are dry). Multiply that weight by 0.12 to get the amount of alum you will need, or by 0.02 to get the correct amount of copper or iron*. Wear gloves, eye protection, and a mask while handling metal powders.
Fill your dye pot with hot tap water, leaving enough room for the fiber.
Weigh out the correct amount of mordant powder and pour it into the dye pot. Mix with a spoon or metal tongs until it has dissolved.
Gently place your wetted fibers into the mordanting solution.
Heat mordant bath to 180F. If you don’t have a candy thermometer, you will have to estimate the temperature. At 180F, steam vapor will be rising off the water but it will not be bubbling. If your mordant bath starts to bubble, turn down the heat.
Maintain heat for 1 hour (alum and copper) or 30 minutes (iron). Stir occasionally to make sure the fibers mordant evenly. If they do not, the dye will take better in some places than others.
After 1 hour (alum and copper) or 30 minutes (iron), remove from heat and allow to cool. Fibers can be left to steep in an alum or copper bath overnight to improve mordant penetration. This can be useful when dyeing thick or tightly woven fabrics. However, fibers should be removed from an iron bath as quickly as possible to prevent corrosion or damage.
Remove cooled fibers. Wearing rubber gloves, gently squeeze excess mordant solution back into the pot. Rinse well in lukewarm water. The fiber does not need to be washed with detergent, but any excess mordant should be rinsed out. This is especially important for iron, because unbonded particles can damage the fiber if they are not washed off.
Set rinsed mordanted fibers aside until ready to dye. Keep out of reach of children and pets.
Dispose of mordant solution according to local guidelines.
For cellulose fibers (cotton, linen, etc.): Pre-treat with a tannin before mordanting with alum, copper, or iron.
Cellulose fibers are more resistant to mordants than protein fibers, and may require pre-treatment with a tannin to absorb mordants effectively. In our experience, success dyeing cellulose fibers depends very much on the quality of fiber used. Handspun, handloom, and organic cotton and linen tend to take natural dyes well, and you can skip the optional tannin step and still get good results. However, commercial cotton tends to be more resistant to natural dyes, possibly because of industrial finishing. It will often need to undergo a two-step mordanting process.
Scour cellulose fibers well. Traditionally this is done in a highly alkaline soda ash solution, but standard household detergents like Tide© are equally alkaline (PH 11), so we prefer to just toss the fiber in the washing machine on an high-temperature cycle with plenty of detergent.
[OPTIONAL] Apply a clear or light-colored tannin to the scoured fabric. Some good choices are Gallnut Extract, Tara, Sumac, or Myrobalan. To use, fill your dye pot with hot water, dissolve 2-5% WOF of your chosen tannin in the dye bath (check vendor’s instructions—each will need a slightly different WOF) and simmer for an hour. Be very careful to keep the fiber moving around: some tannins have insoluble particles that love to get stuck in fabric, and they can cause splotches later on in the dyeing process. After an hour, let cool, remove fibers and rinse well.
Mordant as described above for protein fibers. Use the same percentages of each mordant: 12% alum, 2% copper, or 2% iron.
*CAUTION: Copper powder (copper sulfate pentahydrate) and iron powder (ferrous sulfate) are both irritants, and may be harmful if ingested. Please read your manufacturer’s safety data sheet (MSDS) before using. Wear gloves, a mask, and eye protection whenever handling metal powders, and do not handle the mordanted fibers with bare hands until they have been rinsed. Keep mordant powders, mordant baths, and unrinsed mordanted fibers away from children and pets.
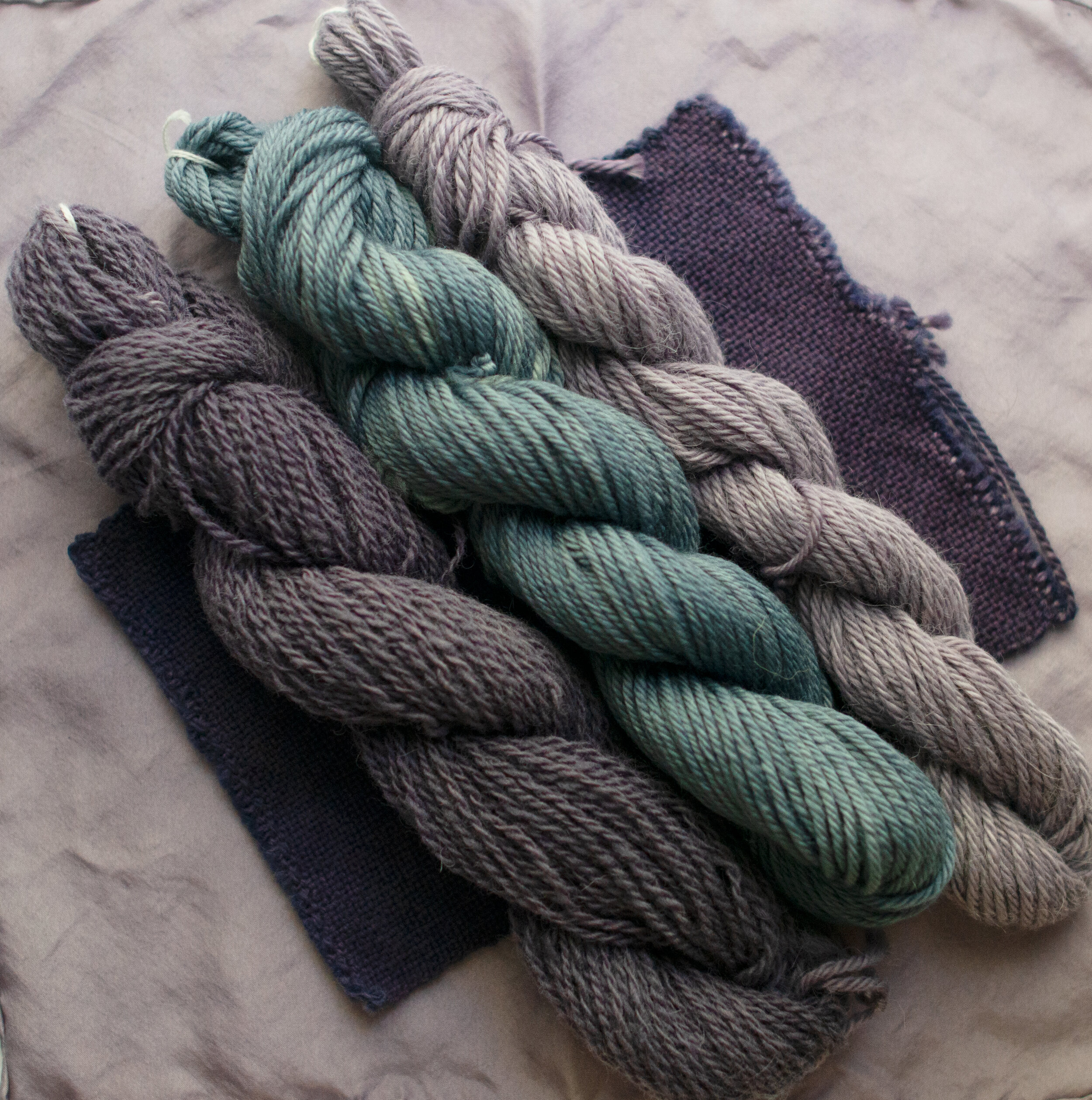
The Recipes.
5. Recipe - Royal Purple
“Royal Purple” is the classic color that logwood gives with an alum mordant. Lighter shades of lavender can be achieved by using a smaller concentration of extract: try it at 0.5% WOF, and after 10 or 15 minutes, add a little more until the fiber has developed the desired shade of purple.
Fill your dye pot with warm water, making sure there is enough room for the fabric to move around and for water to circulate freely.
Adjust the PH to 7 with white vinegar or baking soda. If you don’t have PH strips, just leave as is. Most tap water is fairly close to PH 7.
Weigh out 2% weight-of-fabric (WOF) Royal Logwood Extract into a disposable cup (multiply the dry weight of the fabric by 0.02 to get the correct amount of extract).
Add a little hot water to the cup and mix to form a thin slurry. Make sure to break up any clumps of powder, otherwise they may cause splotches on your fiber.
Pour the slurry into the dyebath and mix well. At this point the dyebath will be deep purple verging on black.
Add your pre-mordanted fibers to the dyebath.
Raise the temperature to 175F and maintain for 30 minutes to 1 hour, stirring every 15 minutes or so to make sure everything dyes evenly. Logwood tends to bond to fiber very quickly, and heating longer than an hour can cause the color to lose clarity.
After 30 minutes to an hour, remove pot from heat and allow to cool.
Remove the fibers and rinse briefly in lukewarm water to remove any particles of dye. You can either proceed immediately to rinsing with detergent, or hang the fabric up to dry first to help the color set. Make sure to hang it up somewhere where dripping dye will cause no damage.
For final rinsing, we recommend using a PH-neutral detergent sold for textile artists, since they are designed to wash out loose dye. Follow the manufacturer’s directions for best results. Be careful using commercial laundry detergents: most are extremely alkaline, and may shift the color of the fabric. CAUTION: Logwood will bleed if not thoroughly rinsed out after dyeing.
Hang up to dry.
NOTE: Results will vary depending on the fiber type and how thoroughly it is mordanted with alum. Very thin fibers like silk habotai will yield lighter colors than yarns and thicker woven fabrics.
6. Recipe - Midnight Blue
The recipe for getting “Midnight Blue” follows the same basic procedure as dyeing purple, the only difference being that it uses copper-mordanted fiber. Logwood has a strong affinity for copper mordants; to get lighter shades of denim blue, use as little as 0.25% WOF.
Fill your dye pot with warm water, making sure there is enough room for the fabric to move around and for water to circulate freely.
Adjust the PH to 7 with white vinegar or baking soda. If you don’t have PH strips, just leave as is. Most tap water is fairly close to PH 7.
Weigh out 2% weight-of-fabric (WOF) Royal Logwood Extract into a disposable cup (multiply the dry weight of the fabric by 0.02 to get the correct amount of extract).
Add a little hot water to the cup and mix to form a thin slurry. Make sure to break up any clumps of powder, otherwise they may cause splotches on your fiber.
Pour the slurry into the dyebath and mix well. At this point the dyebath will be deep purple verging on black.
Add fibers pre-mordanted with 2% weight-of-fabric (WOF) copper to the dyebath.
Raise the temperature to 175F and maintain for 30 minutes to 1 hour, stirring every 15 minutes or so to make sure everything dyes evenly. Logwood will bond to fiber mordanted with copper very quickly, and there is no need to heat longer than an hour.
After 30 minutes to an hour, remove pot from heat and allow to cool.
Remove the fibers and rinse briefly in lukewarm water to remove any particles of dye. You can either proceed immediately to rinsing with detergent, or hang the fabric up to dry first to help the color set. Make sure to hang it up somewhere where dripping dye will cause no damage.
For final rinsing, we recommend using a PH-neutral detergent sold for textile artists, since they are designed to wash out loose dye. Follow the manufacturer’s directions for best results. Be careful using commercial laundry detergents: most are extremely alkaline, and may shift the color of the fabric. CAUTION: Logwood will bleed if not thoroughly rinsed out after dyeing.
Hang up to dry.
NOTE: Logwood on copper can also yield very nice shades of denim blue and gray blues. However, it is very easy to overshoot and get a midnight blue instead. For lighter blues, we recommend weighing out 0.5% WOF into a disposable cup and mixing with hot water to make a slurry. Add 1/3 or 1/2 of the slurry to the dyebath at first. Check the color after 15 minutes; it may already be dark enough. If not, add the rest of the extract.
7. Recipe - Natural Black
One of the reasons logwood was so highly valued in the past is that it is the only direct way to get a natural black. Other recipes for natural blacks involve lengthy overdyeing with three or four different colors to try to mimic true black. Dyeing black is still the main use of logwood today: the same grade of logwood found in Royal Logwood Extract is used by pharmaceutical companies to dye silk medical sutures black.
Fill your dye pot with warm water, making sure there is enough room for the fabric to move around and for water to circulate freely.
Adjust the PH to 7 with white vinegar or baking soda. If you don’t have PH strips, just leave as is. Most tap water is fairly close to PH 7.
Weigh out 4% weight-of-fabric (WOF) Royal Logwood Extract into a disposable cup (multiply the dry weight of the fabric by 0.04 to get the correct amount of extract).
Add a little hot water to the cup and mix to form a thin slurry. Make sure to break up any clumps of powder, otherwise they may cause splotches on your fiber.
Pour the slurry into the dyebath and mix well. At this point the dyebath will be deep purple verging on black.
Add fibers pre-mordanted with 2-3% weight-of-fabric (WOF) iron to the dyebath.
Raise the temperature to 175F and maintain for 45 minutes to 1 hour, stirring every 15 minutes or so to make sure everything dyes evenly.
After 45 minutes to an hour, remove pot from heat and allow to cool.
Remove the fibers and rinse briefly in lukewarm water to remove any particles of dye. You can either proceed immediately to rinsing with detergent, or hang the fabric up to dry first to help the color set. Make sure to hang it up somewhere where dripping dye will cause no damage.
For final rinsing, we recommend using a PH-neutral detergent sold for textile artists, since they are designed to wash out loose dye. Follow the manufacturer’s directions for best results. Be careful using commercial laundry detergents: most are extremely alkaline, and may shift the color of the fabric. CAUTION: Logwood will bleed if not thoroughly rinsed out after dyeing.
Hang up to dry.
NOTE: Natural Black is best applied to silk, because silk can be mordanted with iron without being damaged. Wool can easily become brittle when it is mordanted in an iron solution, and may lose some of its “hand” (softness). If you do want to dye wool black, we recommend using yarns with a heavy twist, which will stand up better to iron’s potentially corrosive effect.
*All text and images are copyright of Shepherd Textiles, LLC. Do not reproduce without permission and attribution.