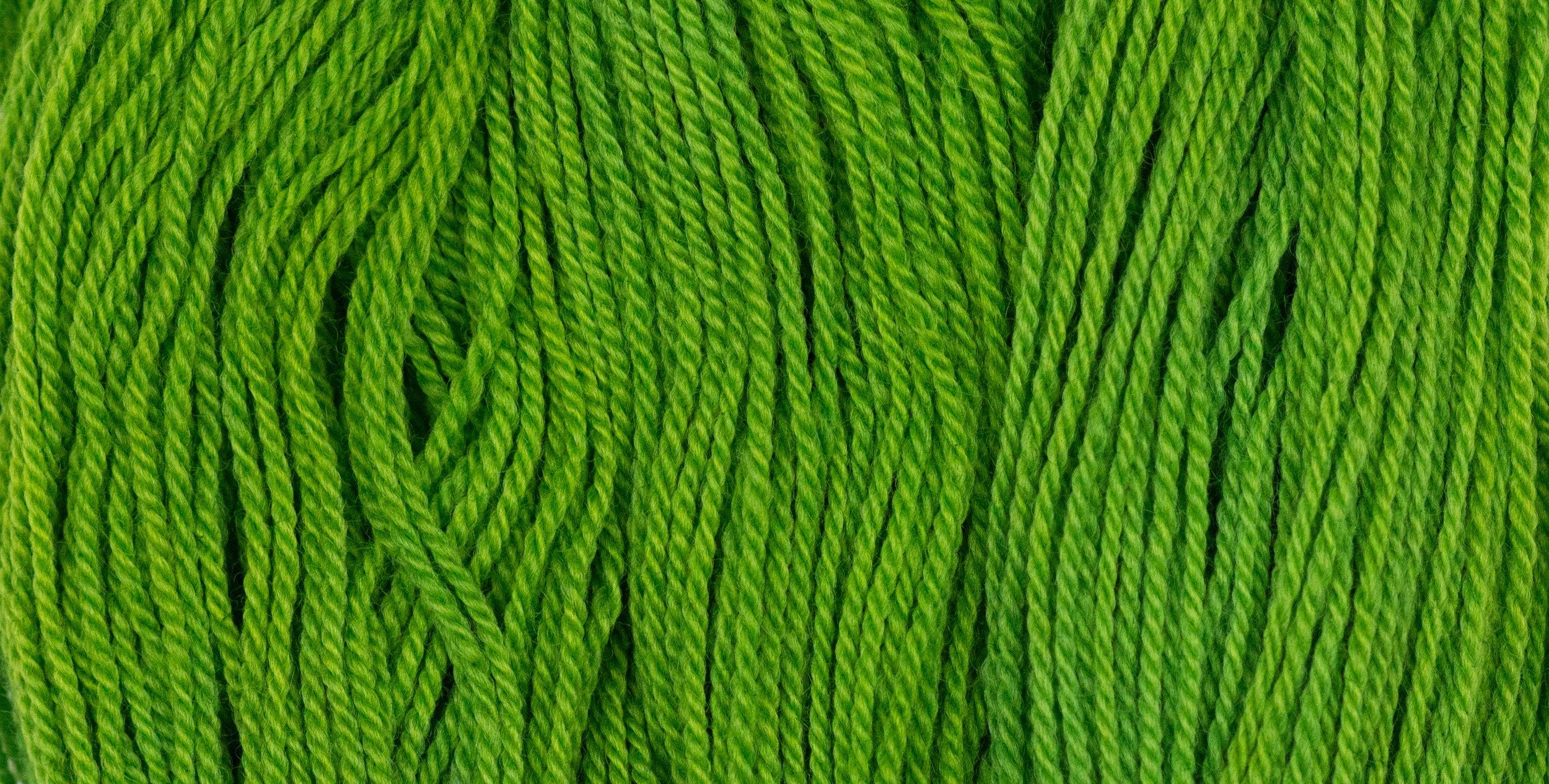
Floral Green™
A Guide to Floral Green™
Shepherd Textiles Floral Green™ is a 100% flower-based natural dye that produces an intense green on woolen fibers. It combines the blue pigment in Gardenia Blue with a proprietary blend of our yellow flower-based extracts to produce a beautiful shade of emerald or shamrock green. Since all the dyes are combined in the same dyebath it is easy to use and does not require overdyeing or multiple baths. Use at 4% weight-of-fabric (WOF) on wool mordanted with alum for the best results. Note that Floral Green™ is not suitable for use on plant fibers like cotton and linen — for plant fibers we recommend Mulberry Leaf Extract instead.
1. Background on Floral Green™
The natural world is awash in good yellow and red pigments — there are countless flowers, roots, and woods that contain natural flavonoids and anthraquinones which will dye textile fibers some shade of yellow or red. However, it is far more rare to find a natural green dye that will work on textile fibers, in spite of the fact that plant life is bursting with green. In some parts of the world it is indeed traditional to use various green leaves, plants, and grasses, but the problem with all these chlorophyll-based dyes is that they quickly degrade on exposure to light and turn yellow or brown. As a result, dyers have been on the search for good natural green dyes for many centuries. Hummel (1896:78), in his survey of the world’s natural green and blue dyes, identified exactly one true direct green dye: a Chinese product called “Lo Kao” which was made through some complex and secret method from buckthorn bark and which has since been lost to time. He lamented that “the number of natural green dyes is very small indeed” (ibid). In the century since Hummel wrote those words, the only additional direct green to find common use is chlorophyllin — otherwise the number of greens remains remarkably limited.
Floral Green™ is the Shepherd Textiles contribution to the search for a good natural green. We combined a blue flower-based dye with some of our yellow flower extracts to create a 100% flower-based natural green for woolen fibers. The blue pigment in Floral Green™ is Gardenia Blue. Gardenia Blue is produced from the fruit of the cape jasmine, gardenia jasminoides, a flowering shrub native to southern China. The dried fruit has been used as a natural yellow dye for many centuries. In the late 1980s, however, a Japanese scientist discovered that one of the compounds in cape jasmine could be converted to a blue pigment (see Cho et al. 2006:230; Hobbs et al. 2018:696). The process involves reacting genipin in the fruit with one of the basic amino acids, like glycine (found in legumes) or tyrosine (found in cheese). This leads to the formation of a blue pigment often referred to as Gardenia Blue. We combined Gardenia Blue with yellow flower dyes that work well under the same dye bath parameters, and then experimented and adjusted the proportions until we arrived at a dye that gives a bright emerald or shamrock green on woolen fibers mordanted with alum. We love the color and we hope you will too.
Solving The Natural Green Puzzle
2. Safety Precautions
DO NOT INGEST. This product is intended for textile dyeing, not as an herbal supplement.
Always wear gloves, a mask, and eye protection when working with dry pigment powders.
Work in a well-ventilated space. Avoid inhaling the steam or vapor from hot mordant baths and dye baths, and keep a lid on the dye pot when possible.
Open jar carefully to avoid spills or creating dust.
Avoid eye contact. If eye contact occurs, rinse with cool water.
Not for use as a cosmetic additive; do not apply directly to skin or hair.
If a spill occurs, quickly wipe up with a paper towel or disposable rag.
Use only dye pots and utensils dedicated to dyeing. Do not use any pots, containers, spoons, tongs, thermometers, or other utensils that will be used for food preparation.
Floral Green™ powder, and all dye baths and mordant liquors made while dyeing, should be kept out of reach of children and pets. Use only with adult supervision.
Shepherd Textiles, LLC is not liable for any misuse of this product or any unintended staining of your clothing, workspace, or other property. Use only as directed.
3. Recommended Supplies
Dye pot. Use a dye pot large enough to hold all your fibers, with plenty of room for them to move around and for the liquid to circulate freely.
Metal tongs. A pair of tongs is useful for stirring and taking fabric out. Use tongs dedicated to dyeing, and not for food preparation.
Rubber gloves. Wear rubber gloves while handling mordanted/dyed fiber before it has been rinsed.
Candy thermometer. The best way to keep track of temperature is to use a candy thermometer that clips to the side of the dye pot.
Scale. Use a scale to weigh out fiber, mordant, and dyestuff.
Alum mordant. The alum usually used for mordanting is aluminum potassium sulfate, also known as potash alum. It is the same alum that you can find in a jar in the spice section at the grocery store.
4. Preparation: Pre-Mordant with Alum
Floral Green™ requires the use of an alum mordant for the best results. Be sure to weigh your fibers while they are still dry, before you begin scouring, so that you can calculate the correct amount of mordant and dye to be used later. It is also important to make sure the fibers are fully wetted through before they go into the mordant bath, so that the mordant penetrates them deeply and evenly.
For wool: Mordant with 10% WOF alum and 11% WOF cream of tartar.
Weigh out woollen fibers you plan to dye (while they are dry). Multiply that weight by 0.10 to get the amount of alum you will need and by 0.11 to get the correct amount of cream of tartar.
Scour the wool before mordanting. Fill a dye pot with enough warm water for your fibers to move around freely. Add 1 tsp of pH-neutral soap per pound of wool being scoured (we use Synthrapol). Raise the heat to 180F and maintain for an hour. After an hour, turn off the heat and let the wool cool until it is safe to handle. Transfer to a hot rinsing bath and rinse in one or two changes of water until all soap suds are rinsed out.
Fill your dye pot with enough hot tap water for your fibers to move around freely.
Weigh out the correct amount of cream of tartar and pour it into the pot. Mix well until dissolved.
Weigh out the correct amount of alum and pour it into the dye pot. Mix well until dissolved.
Gently place your woolen fibers into the mordanting solution.
Gradually heat the mordant bath to 200F, cover, and maintain the heat for 1 hour. Stir every 15 or 20 minutes to make sure fibers mordant evenly. If they do not, the dye may take better in some places than others.
After an hour, remove from heat and let cool until safe enough to handle.
When ready to rinse, transfer the woolen fibers to a hot rinsing bath (without any soap). Rinse well in one or two changes of hot water to remove excess mordant and cream of tartar.
Dispose of the mordant solution according to local guidelines.
For silk: Mordant at 12% WOF with aluminum lactate.
Weigh out the silk fibers you plan to dye (while they are dry). Multiply that weight by 0.12 to get the amount of aluminum lactate you will need.
Scour the silk before mordanting. Fill a dye pot with enough warm water for your fibers to move around freely. Add 1 tsp of pH-neutral soap per pound of silk being scoured (we use Synthrapol). Raise the heat to 160F and maintain for an hour. After an hour, turn off the heat and let the silk cool until it is safe to handle. Transfer to a hot rinsing bath and rinse in one or two changes of water until all soap suds are rinsed out.
Fill your dye pot with hot tap water, leaving enough room for the fiber.
Weigh out the correct amount of aluminum lactate and pour it into the dye pot. Mix well until it has dissolved [Note: You can use an equal quantity of standard alum in place of the aluminum lactate, but aluminum lactate gives the best results].
Gently place your fibers into the mordanting solution.
Heat mordant bath to 160F and maintain heat for 1 hour. Stir every 15 or 20 minutes to make sure fibers mordant evenly. If they do not, the dye will take better in some places than others.
After an hour, remove from heat and let cool to room temperature. Steep for 12 hours or overnight in the mordant bath. Move the silk fibers around occasionally to make sure that no resists form (areas like folds or ties where the mordant does not penetrate as well).
When ready to rinse, put on rubber gloves and gently squeeze excess mordant solution back into the pot. Rinse fibers well in lukewarm water.
For best results, do not allow the mordanted silk to dry out all the way before it is dyed; this may result in an uneven or splotchy dye job.
Dispose of the mordant solution according to local guidelines.
For cellulose fibers (cotton, linen, etc.): Use an alternate green dye, such as Mulberry Leaf Extract.
Unfortunately, Floral Green is not suitable for use on plant fibers like cotton and linen. The problem is that the blue pigment in Floral Green requires an acidic dyebath, but plant fibers like cotton dye best in a neutral or slightly alkaline bath. If you try and dye cotton with Floral Green in a neutral bath you will just get yellow, because the yellow flower pigments will attach to the cotton but the blue pigment will not. If you acidify the dyebath to pH 4 (as you would when dyeing wool and silk) the blue pigment will attach very faintly, but then the yellow pigments will be discharged and the color will be muddied. A better option is simply to use an alternate green dye like Mulberry Leaf Extract that works well with cotton.
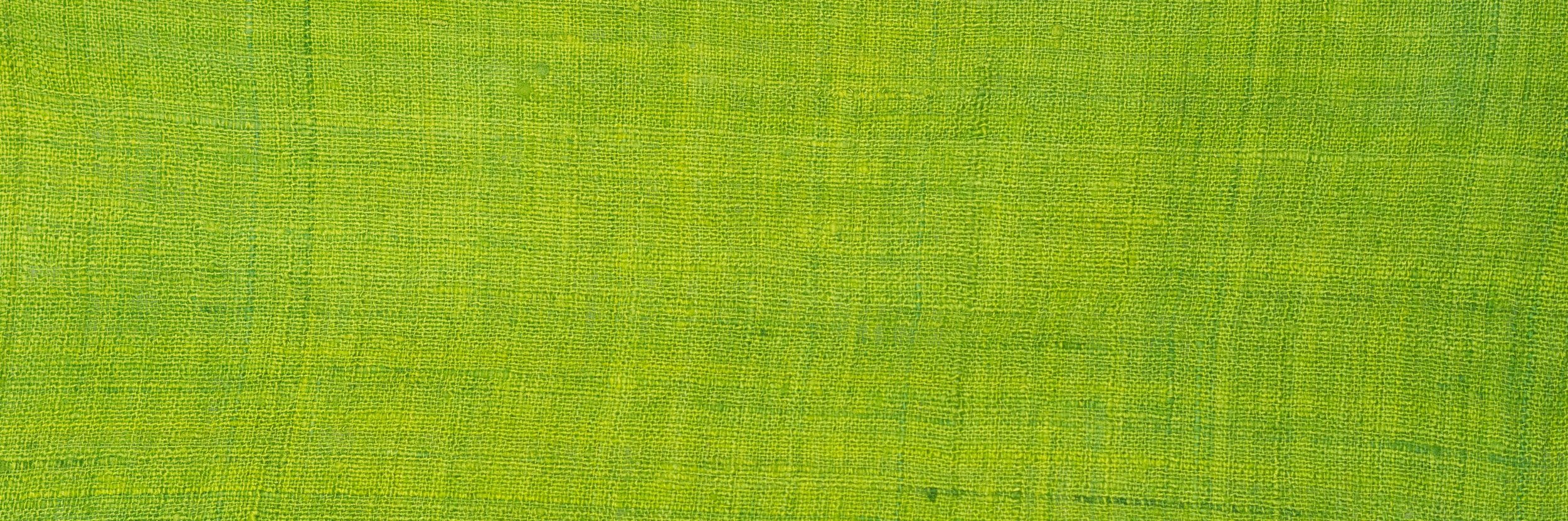
The Recipes
5. Recipe: Emerald on Woolens
Floral Green™ was formulated specifically for this recipe — to produce an intense emerald or shamrock green on woolen fibers mordanted with alum. Note that the gardenia blue pigment in Floral Green bonds to woolen fibers most efficiently in an acidic dyebath at around pH 4, so for best results the dyebath needs to be acidified before the wool is added. The fibers may start out looking fairly blue, then after the bath heats up they may look quite yellow, but after the dyeing is complete the bright green shade will develop.
Fill your dye pot with enough warm water for your fibers to move around freely.
Weigh out the appropriate weight-of-fabric (WOF) of Floral Green powder. Use 1% for a lime green or 4% for emerald green. Add to the dye bath and mix well until any clumps are dissolved. The dye bath should turn an opaque green-blue.
Acidify the dye bath by adding 1 gram of cream of tartar per gallon of water in the bath. Mix well until fully dissolved. This is necessary because the blue pigment in Floral Green bonds to fibers best when the pH is around 4. If the bath is not acidified the blue pigment will not bond as well as the yellow pigments, and the resulting color will be a much more yellowish shade of green [note that if your water source is exceptionally alkaline you may need to add a bit more cream of tartar to get the pH down around 4].
Add your wetted, alum-mordanted wool to the dye bath.
Heat the dyebath to 200F very gradually, over the course of about 30 minutes, stirring regularly so that the wool dyes evenly. Maintain this heat for 1 hour and continue to stir occasionally. After 1 hour, turn off the heat and allow to cool.
When the wool is cool enough to handle safely, remove with tongs and rinse well in warm water with 1 tsp of pH-neutral detergent per pound of wool (we use Synthrapol). Follow the manufacturer’s directions for best results. Rinse again in a few changes of warm water until all soap suds are rinsed out and the water runs clear. CAUTION: Floral Green may bleed if not thoroughly rinsed out after dyeing.
Hang up to dry out of direct sunlight.
6. Recipe: Olive Green on Woolens
Like most natural yellows, the yellow pigments in Floral Green will shift to an olive green shade in the presence of iron. However, the Gardenia Blue pigment does not really change its hue when combined with iron; it stays more or less the same shade of blue. As a result, this recipe produces a very nice blueish shade of olive green, almost like a castelvetrano olive. Although similar results can be achieved by saddening the wool with iron after dyeing, we prefer to pre-mordant with iron instead. Pre-mordanting with iron and plenty of cream of tartar ensures that the iron will not damage the handle (softness) of the wool.
Prepare the wool by mordanting it with iron rather than alum. Follow the directions for mordanting wool in Section 4, but in place of the 10% alum and 11% cream of tartar, use 8% iron (ferrous sulfate) and 12% cream of tartar instead. After mordanting, proceed to the following steps for dyeing.
Fill your dye pot with enough warm water for your fibers to move around freely.
Weigh out 4% weight-of-fabric (WOF) of Floral Green powder. Add to the dye bath and mix well until any clumps are dissolved. The dye bath should turn an opaque green-blue.
Acidify the dye bath by adding 1 gram of cream of tartar per gallon of water in the bath. Mix well until fully dissolved. This is necessary because the blue pigment in Floral Green bonds to fibers best when the pH is around 4. If the bath is not acidified the blue pigment will not bond as well as the yellow pigments, and the resulting color will be a much more yellowish shade of olive green [note that if your water source is exceptionally alkaline you may need to add a bit more cream of tartar to get the pH down around 4].
Add your wetted, iron-mordanted wool to the dye bath.
Heat the dyebath to 200F very gradually, over the course of about 30 minutes, stirring regularly so that the wool dyes evenly. Maintain this heat for 1 hour and continue to stir occasionally. After 1 hour, turn off the heat and allow to cool.
When the wool is cool enough to handle safely, remove with tongs and rinse well in warm water with 1 tsp of pH-neutral detergent per pound of wool (we use Synthrapol). Follow the manufacturer’s directions for best results. Rinse again in a few changes of warm water until all soap suds are rinsed out and the water runs clear. CAUTION: Floral Green may bleed if not thoroughly rinsed out after dyeing.
Hang up to dry out of direct sunlight.
7. Recipe: Green(s) on Silk
Floral Green was formulated for use on woolen fibers but it can also be applied successfully to silk. The color will come out a bit differently, however, because silk will take up the blue and yellow pigments in a different way than wool. Mulberry silk has an a special affinity for the blue pigment in Floral Green so it may come out a slightly bluer shade of green, whereas unbleached wild silks may develop a yellower hue. Note that the dye bath should be acidified in the same way as when dyeing wool.
Fill your dye pot with enough warm water for your fibers to move around freely.
Weigh out the appropriate weight-of-fabric (WOF) of Floral Green powder. Use 5% for thicker weights of silk, or up to 10% for thin silks like satin and habotai. Add to the dye bath and mix well until any clumps are dissolved. The dye bath should turn an opaque green-blue.
Acidify the dye bath by adding 1 gram of cream of tartar per gallon of water in the bath. Mix well until fully dissolved. This is necessary because the blue pigment in Floral Green bonds to fibers best when the pH is around 4. If the bath is not acidified the blue pigment will not bond as well as the yellow pigments, and the resulting color will be a much more yellowish shade of green [note that if your water source is exceptionally alkaline you may need to add a bit more cream of tartar to get the pH down around 4].
Add your wetted, alum-mordanted silk to the dye bath.
Heat the dyebath to 180F very gradually, over the course of about 30 minutes, stirring regularly so that the silk dyes evenly. Maintain this heat for 1 hour and continue to stir occasionally* [see note]. After 1 hour, turn off the heat and allow to cool.
When the silk is cool enough to handle safely, remove with tongs and rinse well in warm water with 1 tsp of pH-neutral detergent per pound of silk (we use Synthrapol). Follow the manufacturer’s directions for best results. Rinse again in a few changes of warm water until all soap suds are rinsed out and the water runs clear. CAUTION: Floral Green may bleed if not thoroughly rinsed out after dyeing.
Hang up to dry out of direct sunlight.
NOTE: Do not be alarmed if, half-way through the dyeing process, it looks like your silk is going to turn out yellow rather than green. The yellow flower pigments in Floral Green tend to bond to fibers more quickly, and at a lower temperature, than the blue pigment, so the fiber may appear mostly yellow during the first part of the dyeing process. The blue will take longer to develop, but by the end of an hour at high temperature it should have bonded to the fiber and the silk should appear green. If not, it is likely that the dye bath was not sufficiently acidic.
All images and text are copyright of Shepherd Textiles, LLC. Do not reproduce without written permission and attribution.